Переходьте в офлайн за допомогою програми Player FM !
C1 Connections: The Innovative Wind Turbine Foundation Interface
Manage episode 446615673 series 2912702
In this Uptime Spotlight, Joel Saxum discusses the C1 Wedge Connection with Managing Director of C1 Connections, Jasper Winkes. They explore how this innovative wind turbine foundation interface addresses challenges in the expanding offshore wind industry, especially for larger turbines. The design benefits include structural enhancements, faster installation, lower maintenance needs, and possible cost savings for both offshore and onshore wind projects.
Sign up now for Uptime Tech News, our weekly email update on all things wind technology. This episode is sponsored by Weather Guard Lightning Tech. Learn more about Weather Guard’s StrikeTape Wind Turbine LPS retrofit. Follow the show on Facebook, YouTube, Twitter, Linkedin and visit Weather Guard on the web. And subscribe to Rosemary Barnes’ YouTube channel here. Have a question we can answer on the show? Email us!
Pardalote Consulting – https://www.pardaloteconsulting.com
Weather Guard Lightning Tech – www.weatherguardwind.com
Intelstor – https://www.intelstor.com
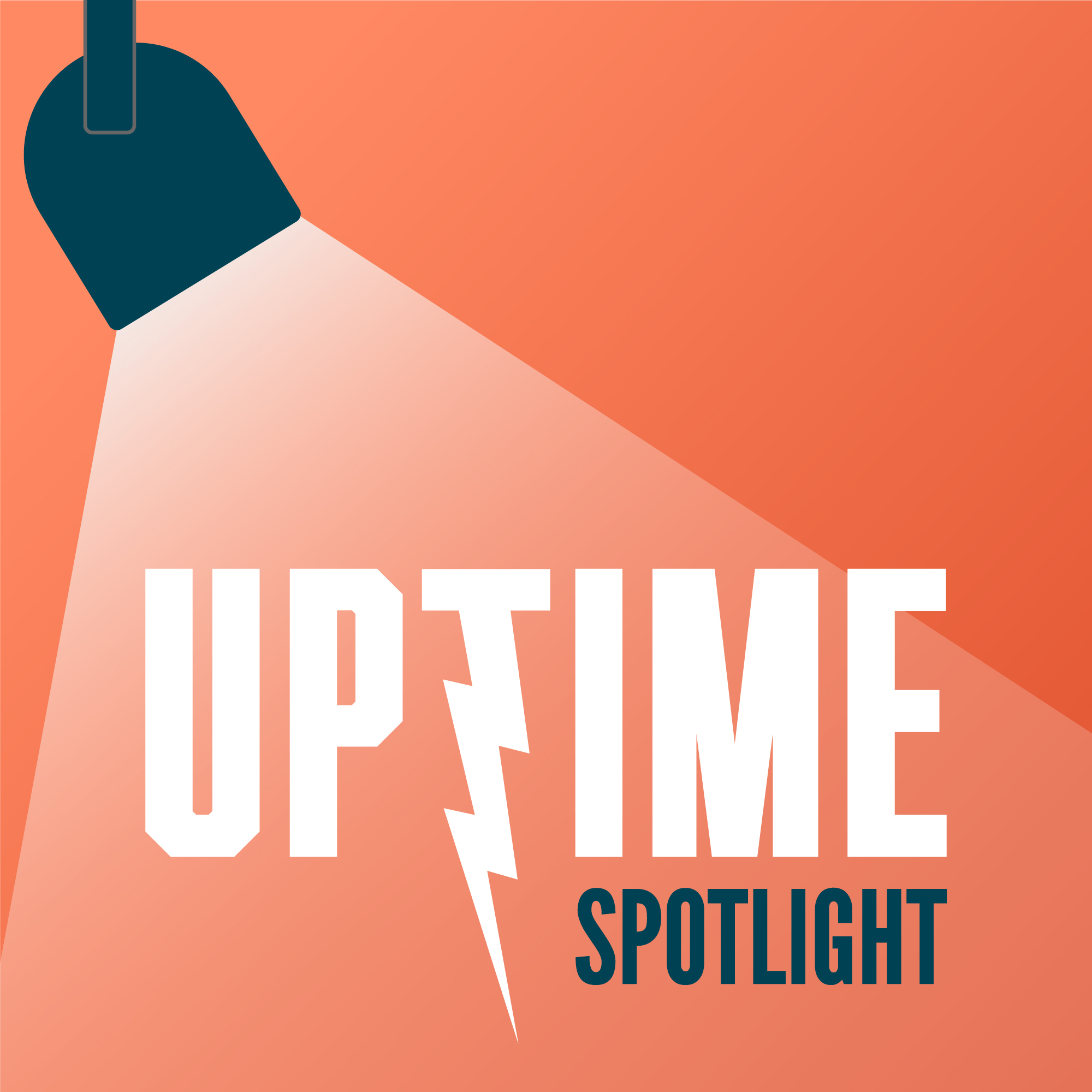
Joel Saxum: I’m Joel Saxum filling in Allen Hall’s shoes as your host for this innovation focused guest episode of the Uptime Wind Energy podcast. Today we’re talking about wind turbines and massively important connections in between the towers and transition pieces. Bolted L flange have been used for decades to connect steel cylindrical structures.
We know this. However, as the wind industry continues to push structural engineering limits with increased capacity for these behemoth wind turbines, specifically offshore, a need for new tech to solve the loading problems has emerged. Enter stage the C1 Wedge Connection. With over seven years of development and two years in the field Jasper Winkes and team have developed the next generation of steel structure connections. Jasper, welcome to the show.
Jasper Winkes: Thank you very much for having me.
Joel Saxum: Great. So we, you and I talked a little bit off air about kind of the technology where it’s been, where it’s coming, where it’s going, but it’s driven by offshore industry trends, right? We’ve all seen, if you look in the North sea, small turbine big, Bigger, all of a sudden now we’re 15 megawatts and some people around the world are talking about what could be the next generation.
What are those trends that are driving your technology?
Jasper Winkes: Yes, indeed. As you mentioned, we’ve seen a massive growth in turbine size over the years. And on one hand, that’s of course the growth of the rotor. And they always say the rotor is the motor. So you need large rotors to extract energy from the wind.
But of course, large rotors also require tall towers. So we see that there’s an exponential increase in overturning moments over the past years whereby essentially the bolted L flange has now reached the point where it is already struggling to deal with the loads and soon will no longer be able to take the loads.
And of course, where that point lies is really project specific but it’s an issue that has been flagged by many industry experts for years already.
That L flange has been used since we started putting steel together hundreds of years ago, so in, but in a turbine, you see the L flange in between every tower section in even up in the tower, some places, right on, in a cell on blades, whatever.
But what we’re focused on is tower connections and even the transition piece and some of that monopile interface. So where, and what are the issues that these, the traditional L flange technology, you explained it to me, maybe you can explain it here to our listeners.
Yeah indeed, we see that the heavy loaded connections, and of course, the more down the substructure, the heavier loaded the connection is, because you’ve got a longer lever arm to where the rotor is pushing on the structure itself.
You see there are overturning moments which are already approaching one giga newton meter. For people to put it in perspective, that’s a 50 kilometer long stick, and then you lift a Tesla at the very end. So it’s massive loads that need to be transferred through these interfaces. And the problems that companies are having is, first of all, there’s a limited number of bolts that you can put on a certain circumference.
So for a bolt at L flange to scale up further, at a certain moment, you cannot fit any more bolts on the circumference. So then the next logical step would be to grow in bolt size. But for a long time, the M72, so a metric dimension stud size was the largest stud in the industry. But we now see a massive base where some companies are considering M80 and even M90.
And that basically brings you into a field where on one hand also your flanges are growing massively in size. But also the tools that you need to handle. We’re talking about tools that can easily weigh 70, 80 or maybe even more kilos. So there’s a real challenge in getting those connections made and then on top of that everything of course needs to be done under time pressure.
Because there’s this expensive installation vessel that needs to wait for either the transition piece or the tower to be connected to the foundation. And we want to solve that issue.
Joel Saxum: Yeah, so the other, you go bigger in bolt size or you need more bolts so then all of a sudden your tower would just start increasing in diameter to a point where it doesn’t, the cost efficiency isn’t there anymore in the tower.
Jasper Winkes: Yeah, so at a certain moment you would have to increase your base diameter, but of course a larger base is exactly in the splash zone attracts more wave loading, which results in more fatigue damage in your foundation. So The optimum is basically not having to increase your interface diameter that much, but still being able to connect it properly.
And our connection technology allows that because you have a higher ultimate capacity, a much higher fatigue capacity, and we can enable both safer and faster installation.
Joel Saxum: Okay, so let’s dive into the technology itself now. I’ve looked online and I’ve checked out some of your white papers and this stuff and it looks to me, you guys have done a great job of marketing the thing because.
From someone who is not a structural engineer, I can look at it and go, okay, that makes sense. But maybe you can explain in better words than that.
Jasper Winkes: Let’s kick off with the reference. The reference is the the L flange, which is essentially two flange bodies, which are connected to a tower and foundation.
So let’s focus on that interface for now. They’re welded at the factories and offshore they need to be connected. So it’s basically a flange that’s protruding inwards into the tower and they are sticking studs in. But it also means that the stud or the bolt is not in the line of the, where the load is transferred.
So it’s an eccentric connection by default. What we have is we also have a flange connection. However, the flanges are different. We have a fork shaped upper flange and a shaft shaped lower flange, which are welded to both the tower and the foundation. And they slide into each other. And then we have a fastener that is radially inserted from the inside of the tower in that fork shaft combination, and thereby pulls the shaft on top of the fork.
And it’s essentially a preloaded connection, with the main difference being that it’s not eccentric. So we have a centric connection, so it’s directly in line with the load transfer path. But we are generating a very high preload with a stud which is basically perpendicular to the load introduction. And we are increasing the load by the means of wedges.
So we are pulling two wedges together that essentially force two bodies apart. And that way people can see it, of course, online how that generates a symmetric preloaded connection.
Joel Saxum: Okay. So I think the, one of the most important things here when I look at this is, okay, if I’m a traditional flange connection, it’s literally on my desk here, I have two coffee cups.
It’s like setting two coffee cups on top of each other. And then the crane has to hold the top piece and you got to figure out how to get the studs or the bolts in and make it all line up, or maybe put some pins in or something. So you have this. this moment or this time during construction or during connection that is I don’t know how to explain it.
It’s a highly critical moment. All hands on deck. Make sure this thing goes perfectly right because you’re not only trying to put load down, but you’re trying to align it to get into the holes correctly. But your technology and like the way you weld the flange on is the way the flanges are designed.
You remove that critical moment where once it sets, it’s. It’s in place.
Jasper Winkes: Yes, indeed. So Indeed, current installation of L flanges has this time critical also safety critical moment where you’re trying to land two flanges and with some kind of pins, they try to line up the holes. We’ve taken that in into consideration when we designed our connection.
So essentially when the upper flange, which is then part of the tower is lowered onto the foundation, there are several guides and bumpers that align the tower directly in the right orientation. Such that the moment that the flanges connect, we have a quick connection system that directly connects the tower to the foundation.
And once that connection has been made, the crane can directly disconnect the tower from the yeah, the tower can be directly released and you can start lifting, for example, your nacelle. So you can save significant amount of time.
Joel Saxum: The safety part of this is a big thing. Talking. To many people in the industry and you watch you see these photos and stuff of a couple of technicians up inside of a tower section and the cranes coming down with a piece and they’re trying to line things up it just seems like We should be more advanced than that as a, as an industry.
And I take from my subsea oil and gas background, right? So subsea oil and gas, almost every single thing that gets connected in the subsea world is connected in the manner that you guys are proposing and when, what your technology is. There’s guide basically, A lot of times it’s as simple as a piece of angle iron.
That’s a guide that brings things on, but there’s a lot of cone, like convex, concave. They all go, they fit together because you don’t have the capability of having people down there or other methods of support. You just have to make sure that when you land the top side or the top piece into the bottom piece, it has to align physically correctly and it has to mate and make a good connection.
So that, idea is what you, it’s not what you’re based on. I’m just trying to put two and two together here. That same concept is exactly what you guys are doing, which you’re increasing speed. So efficiency and installation, you’re decreasing the HSE risk by having this thing basically locked down when it gets there.
And I, and putting less people at risk, I think is the big thing.
Jasper Winkes: Yeah, it’s indeed a, it’s a big thing, which is part of our design by default. Everyone, of course, says that’s yeah, safety is important, but very few people in the end are willing to pay for it. But I think the benefit of our connection is that on one hand, it’s also a lot lighter than a traditional Elf Lounge.
So we’re typically 50 percent lighter and it also allows for significant savings on both the tower as well as the foundation. So in the yeah, basically the total investment is expected to be significantly lower and then If that would also enable much safer installation, it should be a no brainer.
Joel Saxum: Yeah absolutely. So one of the things that you had mentioned to me off air was that when you set that first, or when you set the top piece on, because of the way the connection is, you’re, you have a quick connect method where it’s four bolts and you’re moving on to the next piece.
Jasper Winkes: Indeed. So it’s an X number of of blocks that we insert into the into the flanges that essentially prevent the flanges from from separating again. It’s a little bit like a remotely operated shackle as you probably know from oil and gas.
Joel Saxum: All right. So let’s get into some of the benefits of the technology itself.
First one being reduction of LCOE. And you touched on that a little bit, but it goes a little bit deeper than just the installation phase.
Jasper Winkes: Yeah, so there’s several savings possible. The first one, of course, if you look at design, in MPTP design, we expect significant savings can be made. We’re also working on a large joint industry project that allow a lot of developers to basically learn about those potential savings.
Another point where significant money can be saved is in the maintenance. Because our connection is less sensitive to a preload loss we basically enable in the future for the connection to be fully maintenance free and that I think is the holy grail of connections. So designing something that is very robust and also enables some maintenance free installation.
Joel Saxum: Yeah, because right now you guys this C1 wedge connection is DNV certified, right? But as it sits right now, you guys are still doing, because it’s a new technology, right? It’s been in the field for two years. It doesn’t have the L flange 60 year history as we know. But you, DNV has stated in this certifying right now that you still are visiting it every so often to make sure that all the connections are in place.
Yeah, so DNV,
Jasper Winkes: Takes a precautious stand, which is good because in the end people rely on their expertise which basically indicates that initially you want to do some basically inspections that indeed the connection behaves as it should. But they also understand and they also approve that in the longterm, if indeed the connection behaves as we all expect.
That it can be maintenance free. Yes.
Joel Saxum: Yeah, that’s fantastic because classically, it’s difficult enough onshore to go and do your torque and tensioning, 10 percent or, marking, like going every turbine, going to every flange and checking every bolt to make sure everything is good, that’s difficult enough onshore, now go offshore and you have to get all that tooling, all those people from a sea, from a CTV up onto the transition piece up into the tower, that’s a difficult and very expensive project offshore.
So if in the future. That part of O& M maintenance can be eliminated? Man,
Jasper Winkes: that’s huge.
There’s there’s definitely large potential savings to be made there, yeah.
Joel Saxum: Okay, cool. So then we’ll get a little bit deeper into the technology part of this thing and the engineering, the structural engineering part of it.
Higher ultimate capacity and high fatigue capacity Can you walk us through those concepts with the project? Yeah
Jasper Winkes: Typically our connections are ULS based, meaning that if we have a load set for a specific turbine what is most governing for our design are the extreme loads. So when we know those extreme loads, we know the dimensions of the connection.
We have built a tool that also takes all kind of imperfections to account and we can make a design in a matter of seconds. And what we typically see, that because our design is ULS governed that very same design then basically only needs to go through all the fatigue checks. And we typically see that fatigue is not governing the design, which is unlike a bolted L flange connection, where it’s continuously a battle between ultimate and fatigue capacity.
And now and then companies even need to take shortcuts whereby they have to go towards mailing flanges in order for yeah, the connection to survive the fatigue life. To me, it
Joel Saxum: just makes sense. I think that the future of the wind industry needs innovation like this, right? There’s, there hasn’t been very many step changes in innovation offshore in from what I’ve seen now.
Of course, I’m, I don’t see every corner of the market or everything everybody’s doing. But every turbine, say even the ones that are being installed in the United States right now, and the ones that are being installed in Taiwan, the ones in the North Sea, everything kind of looks the same. The vessels are the same, but this is something different.
So let me rewind a little bit and ask you. How did you come up with this problem statement? Why did this project start? Where did C1 Wedge Connection come from?
Jasper Winkes: Yeah I was visiting conferences, which were about foundations. And at those conferences, there was continuously discussion about the issues around the Bolt at Elf Lodge.
So that sort of planted a seed towards potential improvements, and in the end led to to to this connection being developed. We’ve worked very close together with one of the largest offshore OEMs. We also have a very close collaboration with Delft University here in the Netherlands and I have a great team working with me on this on this solution.
So over the years we’ve spent. Tens of thousands of hours engineering and testing this solution. And it is very convincing and we also get that as feedback from the market. But of course there’s a large investment, which is placed and relies on the structural integrity of this connection. So we are basically being scrutinized to an extreme detail.
You could even say the level of scrutiny is significantly higher than flange because that was already the state of the art. But it’s okay. I fully understand it. And so far we’re only getting very positive
Joel Saxum: reactions. Oh, fantastic. So what we’ve seen is seven years of development, two years in the field.
So what does the future look like for the C1 wedge connection?
Jasper Winkes: We have several projects upcoming that will also be announced in the media once we are allowed to to say something about it. But it’s quite clear that larger turbines require heavy capacity connections, high capacity connections and that’s exactly what we can deliver.
And for us, it’s a matter of convincing all those developers that have joined our joint industry project of the structural integrity by actually delivering a full scale connection, showing how fast we can make that connection, how easy it is. And also of course, show the cost savings that can be obtained by using this kind of connection and all that will basically yeah, pave the route for implementation.
I love it.
Joel Saxum: So we’re talking cheaper, which is always good. High capacity, faster installations, safer installations and less O& M spend in the future. To me that sounds like a home run for an innovation for offshore wind. So Jasper, if someone wants to get a hold of you guys in the C one Connections team, how do they do it?
Jasper Winkes: You can go to our website, so it’s www.c1connections.com. And you can contact us through the website. Also if there are any developers interested in the joint industry project, we’d be happy to inform you. Yeah, and in general the technology directly allows these kind of savings, but also for certain onshore projects.
If you, for example, have locations where you have limitations in terms of tower diameter this connection allows you to basically hold on to that slender tower that still passes under the bridges and doesn’t require a T flange at a height of 20, 30 meters up in the air. So it’s both offshore and onshore that we’re focusing on.
Joel Saxum: Oh, that’s fantastic. Yeah, in the onshore world some of these wind farms that are like, we talked about the Sunzea wind farm that’s going up in the United States right now. That’s 3. 6 gigawatts. There’s going to be hundreds and hundreds of turbines out there. And if you’re able to increase the efficiency at which they’re put together and decrease O& M costs in the future, I think this technology should be implemented onshore as well.
Of course
Jasper Winkes: The biggest pain right now is is offshore. So that’s where we’re focusing on. But we see definitely a lot of traction in the onshore market as well. So yeah, bring
Joel Saxum: it on. Bring it on. I love it. Jasper, thanks for joining me here today on the Uptime Podcast and best of luck in the future.
Thank you very much for having us.
372 епізодів
Manage episode 446615673 series 2912702
In this Uptime Spotlight, Joel Saxum discusses the C1 Wedge Connection with Managing Director of C1 Connections, Jasper Winkes. They explore how this innovative wind turbine foundation interface addresses challenges in the expanding offshore wind industry, especially for larger turbines. The design benefits include structural enhancements, faster installation, lower maintenance needs, and possible cost savings for both offshore and onshore wind projects.
Sign up now for Uptime Tech News, our weekly email update on all things wind technology. This episode is sponsored by Weather Guard Lightning Tech. Learn more about Weather Guard’s StrikeTape Wind Turbine LPS retrofit. Follow the show on Facebook, YouTube, Twitter, Linkedin and visit Weather Guard on the web. And subscribe to Rosemary Barnes’ YouTube channel here. Have a question we can answer on the show? Email us!
Pardalote Consulting – https://www.pardaloteconsulting.com
Weather Guard Lightning Tech – www.weatherguardwind.com
Intelstor – https://www.intelstor.com
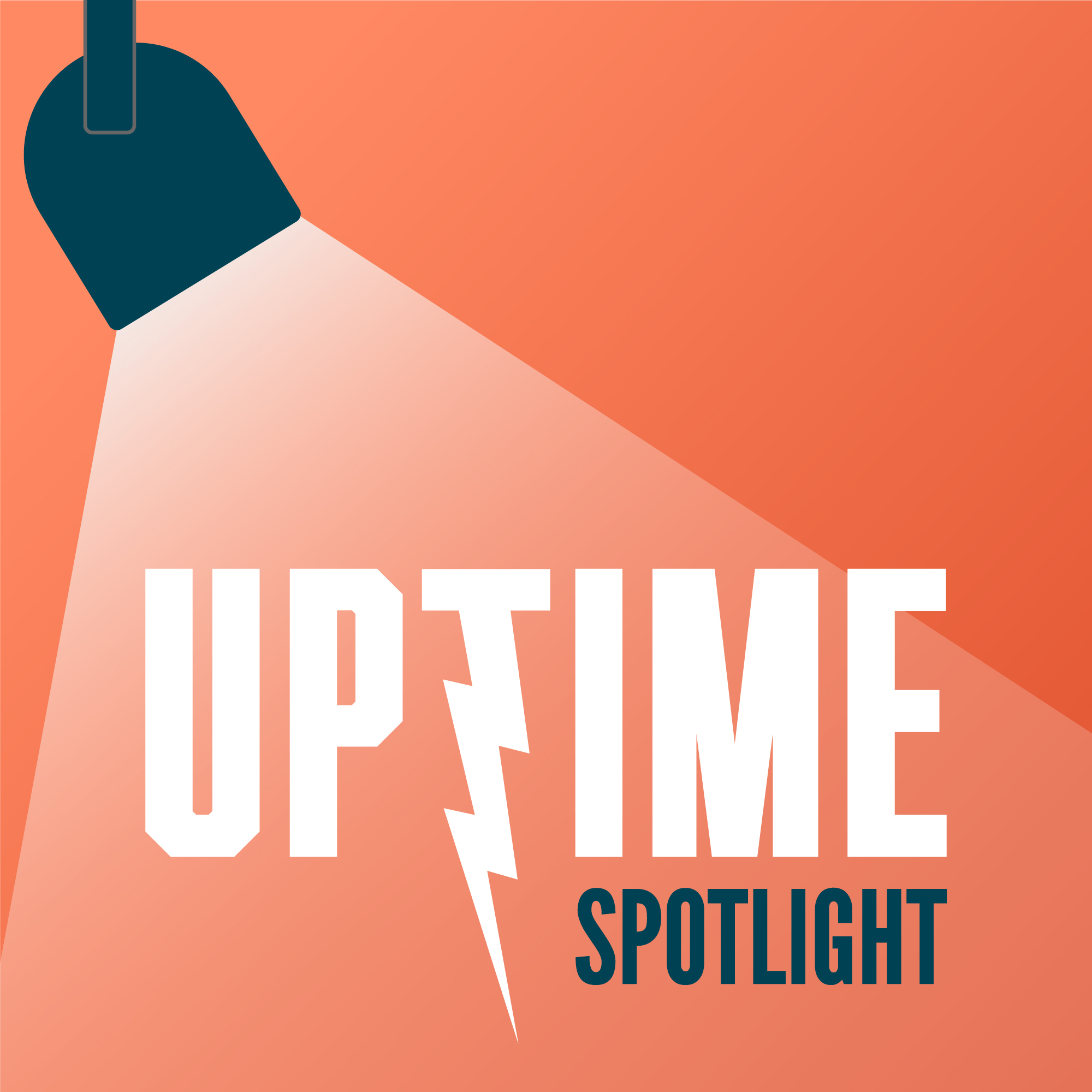
Joel Saxum: I’m Joel Saxum filling in Allen Hall’s shoes as your host for this innovation focused guest episode of the Uptime Wind Energy podcast. Today we’re talking about wind turbines and massively important connections in between the towers and transition pieces. Bolted L flange have been used for decades to connect steel cylindrical structures.
We know this. However, as the wind industry continues to push structural engineering limits with increased capacity for these behemoth wind turbines, specifically offshore, a need for new tech to solve the loading problems has emerged. Enter stage the C1 Wedge Connection. With over seven years of development and two years in the field Jasper Winkes and team have developed the next generation of steel structure connections. Jasper, welcome to the show.
Jasper Winkes: Thank you very much for having me.
Joel Saxum: Great. So we, you and I talked a little bit off air about kind of the technology where it’s been, where it’s coming, where it’s going, but it’s driven by offshore industry trends, right? We’ve all seen, if you look in the North sea, small turbine big, Bigger, all of a sudden now we’re 15 megawatts and some people around the world are talking about what could be the next generation.
What are those trends that are driving your technology?
Jasper Winkes: Yes, indeed. As you mentioned, we’ve seen a massive growth in turbine size over the years. And on one hand, that’s of course the growth of the rotor. And they always say the rotor is the motor. So you need large rotors to extract energy from the wind.
But of course, large rotors also require tall towers. So we see that there’s an exponential increase in overturning moments over the past years whereby essentially the bolted L flange has now reached the point where it is already struggling to deal with the loads and soon will no longer be able to take the loads.
And of course, where that point lies is really project specific but it’s an issue that has been flagged by many industry experts for years already.
That L flange has been used since we started putting steel together hundreds of years ago, so in, but in a turbine, you see the L flange in between every tower section in even up in the tower, some places, right on, in a cell on blades, whatever.
But what we’re focused on is tower connections and even the transition piece and some of that monopile interface. So where, and what are the issues that these, the traditional L flange technology, you explained it to me, maybe you can explain it here to our listeners.
Yeah indeed, we see that the heavy loaded connections, and of course, the more down the substructure, the heavier loaded the connection is, because you’ve got a longer lever arm to where the rotor is pushing on the structure itself.
You see there are overturning moments which are already approaching one giga newton meter. For people to put it in perspective, that’s a 50 kilometer long stick, and then you lift a Tesla at the very end. So it’s massive loads that need to be transferred through these interfaces. And the problems that companies are having is, first of all, there’s a limited number of bolts that you can put on a certain circumference.
So for a bolt at L flange to scale up further, at a certain moment, you cannot fit any more bolts on the circumference. So then the next logical step would be to grow in bolt size. But for a long time, the M72, so a metric dimension stud size was the largest stud in the industry. But we now see a massive base where some companies are considering M80 and even M90.
And that basically brings you into a field where on one hand also your flanges are growing massively in size. But also the tools that you need to handle. We’re talking about tools that can easily weigh 70, 80 or maybe even more kilos. So there’s a real challenge in getting those connections made and then on top of that everything of course needs to be done under time pressure.
Because there’s this expensive installation vessel that needs to wait for either the transition piece or the tower to be connected to the foundation. And we want to solve that issue.
Joel Saxum: Yeah, so the other, you go bigger in bolt size or you need more bolts so then all of a sudden your tower would just start increasing in diameter to a point where it doesn’t, the cost efficiency isn’t there anymore in the tower.
Jasper Winkes: Yeah, so at a certain moment you would have to increase your base diameter, but of course a larger base is exactly in the splash zone attracts more wave loading, which results in more fatigue damage in your foundation. So The optimum is basically not having to increase your interface diameter that much, but still being able to connect it properly.
And our connection technology allows that because you have a higher ultimate capacity, a much higher fatigue capacity, and we can enable both safer and faster installation.
Joel Saxum: Okay, so let’s dive into the technology itself now. I’ve looked online and I’ve checked out some of your white papers and this stuff and it looks to me, you guys have done a great job of marketing the thing because.
From someone who is not a structural engineer, I can look at it and go, okay, that makes sense. But maybe you can explain in better words than that.
Jasper Winkes: Let’s kick off with the reference. The reference is the the L flange, which is essentially two flange bodies, which are connected to a tower and foundation.
So let’s focus on that interface for now. They’re welded at the factories and offshore they need to be connected. So it’s basically a flange that’s protruding inwards into the tower and they are sticking studs in. But it also means that the stud or the bolt is not in the line of the, where the load is transferred.
So it’s an eccentric connection by default. What we have is we also have a flange connection. However, the flanges are different. We have a fork shaped upper flange and a shaft shaped lower flange, which are welded to both the tower and the foundation. And they slide into each other. And then we have a fastener that is radially inserted from the inside of the tower in that fork shaft combination, and thereby pulls the shaft on top of the fork.
And it’s essentially a preloaded connection, with the main difference being that it’s not eccentric. So we have a centric connection, so it’s directly in line with the load transfer path. But we are generating a very high preload with a stud which is basically perpendicular to the load introduction. And we are increasing the load by the means of wedges.
So we are pulling two wedges together that essentially force two bodies apart. And that way people can see it, of course, online how that generates a symmetric preloaded connection.
Joel Saxum: Okay. So I think the, one of the most important things here when I look at this is, okay, if I’m a traditional flange connection, it’s literally on my desk here, I have two coffee cups.
It’s like setting two coffee cups on top of each other. And then the crane has to hold the top piece and you got to figure out how to get the studs or the bolts in and make it all line up, or maybe put some pins in or something. So you have this. this moment or this time during construction or during connection that is I don’t know how to explain it.
It’s a highly critical moment. All hands on deck. Make sure this thing goes perfectly right because you’re not only trying to put load down, but you’re trying to align it to get into the holes correctly. But your technology and like the way you weld the flange on is the way the flanges are designed.
You remove that critical moment where once it sets, it’s. It’s in place.
Jasper Winkes: Yes, indeed. So Indeed, current installation of L flanges has this time critical also safety critical moment where you’re trying to land two flanges and with some kind of pins, they try to line up the holes. We’ve taken that in into consideration when we designed our connection.
So essentially when the upper flange, which is then part of the tower is lowered onto the foundation, there are several guides and bumpers that align the tower directly in the right orientation. Such that the moment that the flanges connect, we have a quick connection system that directly connects the tower to the foundation.
And once that connection has been made, the crane can directly disconnect the tower from the yeah, the tower can be directly released and you can start lifting, for example, your nacelle. So you can save significant amount of time.
Joel Saxum: The safety part of this is a big thing. Talking. To many people in the industry and you watch you see these photos and stuff of a couple of technicians up inside of a tower section and the cranes coming down with a piece and they’re trying to line things up it just seems like We should be more advanced than that as a, as an industry.
And I take from my subsea oil and gas background, right? So subsea oil and gas, almost every single thing that gets connected in the subsea world is connected in the manner that you guys are proposing and when, what your technology is. There’s guide basically, A lot of times it’s as simple as a piece of angle iron.
That’s a guide that brings things on, but there’s a lot of cone, like convex, concave. They all go, they fit together because you don’t have the capability of having people down there or other methods of support. You just have to make sure that when you land the top side or the top piece into the bottom piece, it has to align physically correctly and it has to mate and make a good connection.
So that, idea is what you, it’s not what you’re based on. I’m just trying to put two and two together here. That same concept is exactly what you guys are doing, which you’re increasing speed. So efficiency and installation, you’re decreasing the HSE risk by having this thing basically locked down when it gets there.
And I, and putting less people at risk, I think is the big thing.
Jasper Winkes: Yeah, it’s indeed a, it’s a big thing, which is part of our design by default. Everyone, of course, says that’s yeah, safety is important, but very few people in the end are willing to pay for it. But I think the benefit of our connection is that on one hand, it’s also a lot lighter than a traditional Elf Lounge.
So we’re typically 50 percent lighter and it also allows for significant savings on both the tower as well as the foundation. So in the yeah, basically the total investment is expected to be significantly lower and then If that would also enable much safer installation, it should be a no brainer.
Joel Saxum: Yeah absolutely. So one of the things that you had mentioned to me off air was that when you set that first, or when you set the top piece on, because of the way the connection is, you’re, you have a quick connect method where it’s four bolts and you’re moving on to the next piece.
Jasper Winkes: Indeed. So it’s an X number of of blocks that we insert into the into the flanges that essentially prevent the flanges from from separating again. It’s a little bit like a remotely operated shackle as you probably know from oil and gas.
Joel Saxum: All right. So let’s get into some of the benefits of the technology itself.
First one being reduction of LCOE. And you touched on that a little bit, but it goes a little bit deeper than just the installation phase.
Jasper Winkes: Yeah, so there’s several savings possible. The first one, of course, if you look at design, in MPTP design, we expect significant savings can be made. We’re also working on a large joint industry project that allow a lot of developers to basically learn about those potential savings.
Another point where significant money can be saved is in the maintenance. Because our connection is less sensitive to a preload loss we basically enable in the future for the connection to be fully maintenance free and that I think is the holy grail of connections. So designing something that is very robust and also enables some maintenance free installation.
Joel Saxum: Yeah, because right now you guys this C1 wedge connection is DNV certified, right? But as it sits right now, you guys are still doing, because it’s a new technology, right? It’s been in the field for two years. It doesn’t have the L flange 60 year history as we know. But you, DNV has stated in this certifying right now that you still are visiting it every so often to make sure that all the connections are in place.
Yeah, so DNV,
Jasper Winkes: Takes a precautious stand, which is good because in the end people rely on their expertise which basically indicates that initially you want to do some basically inspections that indeed the connection behaves as it should. But they also understand and they also approve that in the longterm, if indeed the connection behaves as we all expect.
That it can be maintenance free. Yes.
Joel Saxum: Yeah, that’s fantastic because classically, it’s difficult enough onshore to go and do your torque and tensioning, 10 percent or, marking, like going every turbine, going to every flange and checking every bolt to make sure everything is good, that’s difficult enough onshore, now go offshore and you have to get all that tooling, all those people from a sea, from a CTV up onto the transition piece up into the tower, that’s a difficult and very expensive project offshore.
So if in the future. That part of O& M maintenance can be eliminated? Man,
Jasper Winkes: that’s huge.
There’s there’s definitely large potential savings to be made there, yeah.
Joel Saxum: Okay, cool. So then we’ll get a little bit deeper into the technology part of this thing and the engineering, the structural engineering part of it.
Higher ultimate capacity and high fatigue capacity Can you walk us through those concepts with the project? Yeah
Jasper Winkes: Typically our connections are ULS based, meaning that if we have a load set for a specific turbine what is most governing for our design are the extreme loads. So when we know those extreme loads, we know the dimensions of the connection.
We have built a tool that also takes all kind of imperfections to account and we can make a design in a matter of seconds. And what we typically see, that because our design is ULS governed that very same design then basically only needs to go through all the fatigue checks. And we typically see that fatigue is not governing the design, which is unlike a bolted L flange connection, where it’s continuously a battle between ultimate and fatigue capacity.
And now and then companies even need to take shortcuts whereby they have to go towards mailing flanges in order for yeah, the connection to survive the fatigue life. To me, it
Joel Saxum: just makes sense. I think that the future of the wind industry needs innovation like this, right? There’s, there hasn’t been very many step changes in innovation offshore in from what I’ve seen now.
Of course, I’m, I don’t see every corner of the market or everything everybody’s doing. But every turbine, say even the ones that are being installed in the United States right now, and the ones that are being installed in Taiwan, the ones in the North Sea, everything kind of looks the same. The vessels are the same, but this is something different.
So let me rewind a little bit and ask you. How did you come up with this problem statement? Why did this project start? Where did C1 Wedge Connection come from?
Jasper Winkes: Yeah I was visiting conferences, which were about foundations. And at those conferences, there was continuously discussion about the issues around the Bolt at Elf Lodge.
So that sort of planted a seed towards potential improvements, and in the end led to to to this connection being developed. We’ve worked very close together with one of the largest offshore OEMs. We also have a very close collaboration with Delft University here in the Netherlands and I have a great team working with me on this on this solution.
So over the years we’ve spent. Tens of thousands of hours engineering and testing this solution. And it is very convincing and we also get that as feedback from the market. But of course there’s a large investment, which is placed and relies on the structural integrity of this connection. So we are basically being scrutinized to an extreme detail.
You could even say the level of scrutiny is significantly higher than flange because that was already the state of the art. But it’s okay. I fully understand it. And so far we’re only getting very positive
Joel Saxum: reactions. Oh, fantastic. So what we’ve seen is seven years of development, two years in the field.
So what does the future look like for the C1 wedge connection?
Jasper Winkes: We have several projects upcoming that will also be announced in the media once we are allowed to to say something about it. But it’s quite clear that larger turbines require heavy capacity connections, high capacity connections and that’s exactly what we can deliver.
And for us, it’s a matter of convincing all those developers that have joined our joint industry project of the structural integrity by actually delivering a full scale connection, showing how fast we can make that connection, how easy it is. And also of course, show the cost savings that can be obtained by using this kind of connection and all that will basically yeah, pave the route for implementation.
I love it.
Joel Saxum: So we’re talking cheaper, which is always good. High capacity, faster installations, safer installations and less O& M spend in the future. To me that sounds like a home run for an innovation for offshore wind. So Jasper, if someone wants to get a hold of you guys in the C one Connections team, how do they do it?
Jasper Winkes: You can go to our website, so it’s www.c1connections.com. And you can contact us through the website. Also if there are any developers interested in the joint industry project, we’d be happy to inform you. Yeah, and in general the technology directly allows these kind of savings, but also for certain onshore projects.
If you, for example, have locations where you have limitations in terms of tower diameter this connection allows you to basically hold on to that slender tower that still passes under the bridges and doesn’t require a T flange at a height of 20, 30 meters up in the air. So it’s both offshore and onshore that we’re focusing on.
Joel Saxum: Oh, that’s fantastic. Yeah, in the onshore world some of these wind farms that are like, we talked about the Sunzea wind farm that’s going up in the United States right now. That’s 3. 6 gigawatts. There’s going to be hundreds and hundreds of turbines out there. And if you’re able to increase the efficiency at which they’re put together and decrease O& M costs in the future, I think this technology should be implemented onshore as well.
Of course
Jasper Winkes: The biggest pain right now is is offshore. So that’s where we’re focusing on. But we see definitely a lot of traction in the onshore market as well. So yeah, bring
Joel Saxum: it on. Bring it on. I love it. Jasper, thanks for joining me here today on the Uptime Podcast and best of luck in the future.
Thank you very much for having us.
372 епізодів
Усі епізоди
×Ласкаво просимо до Player FM!
Player FM сканує Інтернет для отримання високоякісних подкастів, щоб ви могли насолоджуватися ними зараз. Це найкращий додаток для подкастів, який працює на Android, iPhone і веб-сторінці. Реєстрація для синхронізації підписок між пристроями.